The Back Story
A 70-year-old manufacturer of standard and specialty casters was looking for a company to help them bring automation into their product storage and order fulfillment area. They were looking for a way to bring large heavy totes of completed casters to an area for order picking and then returning the tote back to the shelving area until needed for another order. Additionally, the manufacturer wanted the ability to queue up totes to minimize the wait time for picking products for order pack out.
The Application
The end user turned to one of Alba’s partners, KC Robotics, to provide a solution for automating their plant. Alba worked with to come up with a system which incorporated two (2) over/under conveyor systems, positioned side by side, that would convey totes of finished product, weighing up to 3,000 lb. each, into the robot pick station on the lower level. The robot would then pick the parts required to fulfill the order.
Once the parts had been picked by the robot, the totes would be raised to the upper level via conveyor lift table and conveyed back to the beginning of the line. A fork truck would pick up the tote and return it back to the rack.
When the pick zone conveyor was clear and in the home position, the next tote that was waiting in the queue would be conveyed into the pick zone. This process of conveying totes in and out of the system would continue automatically to process all the orders for the day.

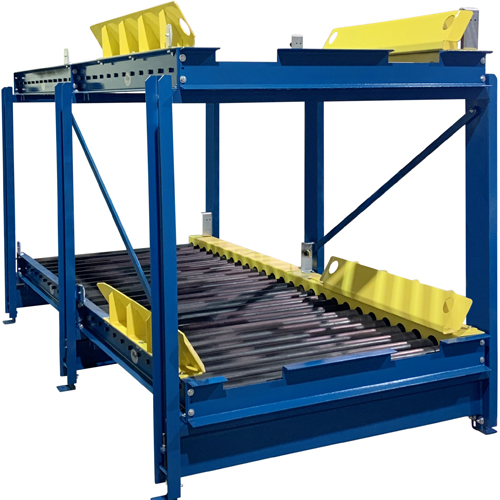
Alba’s Solution
Alba provided multiple sections of standard CDLR conveyor mounted to multi-level poly-tier supports to configure the system for over/under levels. There was enough space left above the lower-level conveyor to allow the tote at 36” tall to run down the conveyor uninhibited. Alba also provided a CDLR mounted to a hydraulic lift table with proximity sensors mounted to an external stand for sensing the infeed, robot interface and discharge levels.
The parallel runs of conveyor were installed next to each other allowing the robot to shift from one lane of parts to another lane without waiting for the next load to be picked. The equipment was manufactured and tested in Alba’s facility before being shipped to KC Robotics for integration and preparation for a FAT (Factory Acceptance Test).
Conveyor Specifications
- Twenty (20) Model 29760-4.5-48 CDLR Conveyors 2-9/16″ x 7 Ga., 48″ EW
- Two (2) Model 29760-4.5-48 CDLR Conveyors mounted to a Hydraulic Lift Table
Resulting Benefit
The implementation of the order picking robot improved safety by minimizing the operators’ handling of heavy totes and eliminated the ergonomic challenges with manual order picking. The new design also increased order processing efficiency meeting the on-going demand for their casters.
The next time you encounter a challenge, call Alba Manufacturing. We can help you locate your nearest Alba Partner Network Member to assist with your next project.
About Us
Alba Manufacturing, established in 1973, engineers and designs heavy-duty roller conveyor systems. Our systems consist of chain driven live roller (CDLR), zero pressure accumulation, drag chain, gravity, lift and rotate, pallet stackers and dispensers, turntables, chain transfers and transfer cars. Our corporate office and manufacturing facility is located in Fairfield, Ohio, approximately 30 minutes north of Cincinnati, Ohio.
For more information regarding this application/solution, please contact us via phone at 866.252.2634; via web at www.albamfg.com or via email at RockSolidConveyor@albamfg.com.