With the onset of the pandemic, our daily habits changed dramatically. While some businesses were devastated, others tried to find alternative ways of generating revenue to keep their doors open. The restaurant industry is a prime example. Take-out food and order-in food have always existed, however order-in food has recently taken on a whole new life. The industry has developed an intricate system of preparing, cooking, and transporting our favorite delights.
According to McKinsey & Company, leading experts in industry trends, “Food delivery has become a global market worth more than $150 billion, having more than tripled since 2017. In the United States, the market has more than doubled during the COVID-19 pandemic, following healthy historical growth of 8 percent.”1 When the lockdowns were most severe, the food-delivery market spiked.
Why is this important? Food containers must be designed, manufactured, and transported to manage the increased order-in and take-out demand. Think about it. We stop at our local grocery store to pick up a salad for lunch, we run the kids over to Taco Bell before practice, or we have our favorite Mexican restaurant deliver dinner for a family gathering. Each of these food options require specifically developed containers and packaging maximizing the items’ stability and freshness.
Simplimatic Automation, a long-time Alba partner, is a robotic integrator and serves various industries. In this case, the end user manufactures plastic containers to serve the food and restaurant industries. The end user’s products were palletized via robot on 40” x 48” GMA pallets with a maximum weight of 2,000 lbs. Simplimatic streamlined their customer’s palletizing area by bringing twelve (12) production lines together into four robotic palletizing cells.
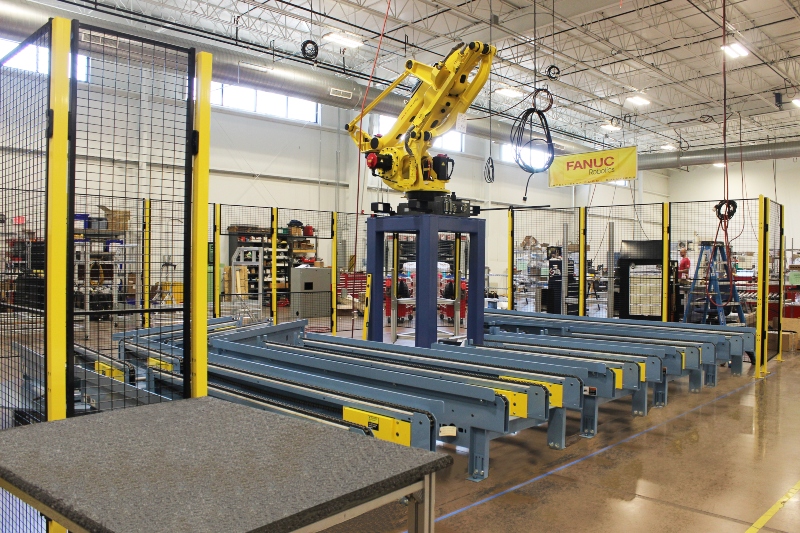
Alba’s portion of the project consisted of an intricate system of twenty-four (24) drag chain conveyors, two (2) pallet dispensers with full controls, and five (5) turntables (one with a pneumatic rotation base and four with motorized rotation bases) with drag chain conveyor mounted on top. Additionally, Alba manufactured two (2) transfer cars to take the finished pallets from the palletizing cells to the stretch wrapper areas.
Alba provided conveyor to enable the streamlining of the end user’s palletizing area which operates 24 hours a day, 7 days a week. Additionally, we made Simplimatic’s life easier by providing our standard fully assembled conveyors decreasing their installation time in the field by 50 percent.
Our heavy-duty pallet handling conveyor integrates seamlessly with robotic and stretch wrap applications.
Conveyor/Product Specifications
- Two-Strand Model RC-80 Drag Chain Conveyor
- Three-Strand Model RC-80 Drag Chain Conveyors (23)
- Two-Pallet Dispensers with Full Controls (2)
- Two-Postion Transfer Cars with a Two-Strand and Three-Strand Drag Chain Conveyor Side-by-Side (2)
- Two-Strand Model RC-80 Drag Chain Conveyor Mounted to a 90° Pneumatic Operated Turntable Base
- Three-Strand Model RC-80 Drag Chain Conveyor Mounted to a 90° Electric Operated Turntable Base (4)
- Elevation: 24″ Top of Chain
- Paint: Pastel Blue
Value-Added Features
Guide Rail, End Stops, Pre-mounted Proximity Switches and Solenoid Valve, Full Controls on the Pallet Dispensers
The next time you encounter a challenge, call Alba Manufacturing. We can help you locate your nearest Alba Partner Network Member to assist with your next project.
About Us
Alba Manufacturing, established in 1973, engineers and designs heavy-duty roller conveyor systems. Our systems consist of chain driven live roller (CDLR), zero pressure accumulation, drag chain, gravity, lift and rotate, pallet stackers and dispensers, turntables, chain transfers and transfer cars. Our corporate office and manufacturing facility is located in Fairfield, Ohio, approximately 30 minutes north of Cincinnati, Ohio.
For more information regarding this application/solution, please contact us via phone at 866.252.2634; via web at www.albamfg.com or via email at RockSolidConveyor@albamfg.com.