The Setup
A system integrator partner came to us with an interesting application. The end user, a lettuce producer, thought they needed stainless steel drag chain conveyors to transport both GMA and CHEP 1,600 lb. pallets of product. The customer had several necessary requirements for the conveyor purchase. One major requirement – reduce or virtually eliminate unreachable surface areas in order to spray down and easily clean equipment during their daily washing routine. Another request – the equipment needed to inhibit rust and not oxidize in the working environment.
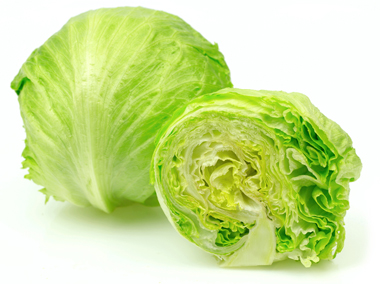
The Challenge
Alba worked with the integrator to provide a 5-strand conveyor design that had open passageways and a reduced number of bolted areas where two surfaces could create traps for moisture.
During equipment wash down, bolted together, uncleanable, large surface areas created hazards that needed to be avoided. Being able to deliver conveyors with an open design and rust resistance was essential and it would be priced well below 100% stainless steel construction. Since the end-product was packaged and didn’t have direct contact with the conveyor system, there wasn’t any need for full stainless steel.
The Solution
Alba developed a design to meet the functional aspects of this project that also met the needs and requests of the end user. Alba provided 5-strand drag chain conveyors with epoxy painted frames and tread plates. The sprockets, axles, and drive shafts were zinc plated. Stainless steel flange bearings were used on the drive shaft per the customer’s request. The conveyors were supplied with SEW Eurodrive gear motors with a Food Industry IP Package which included food grade lubricant, epoxy painted surfaces, and stainless collars. The motors were also sealed to an IP69 rating for environmental protection.
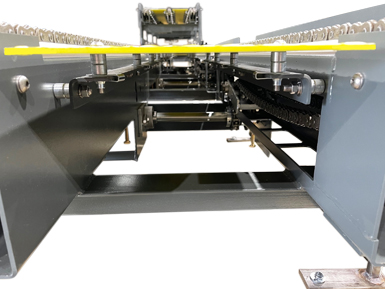
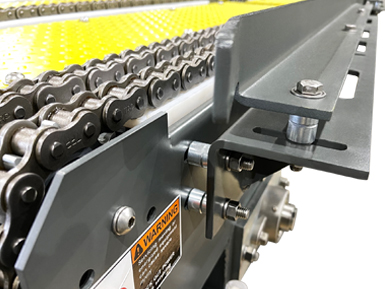
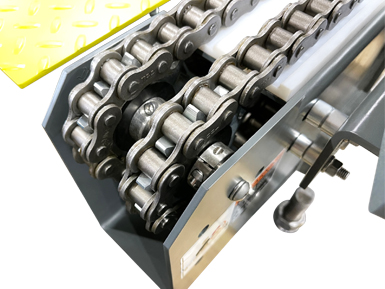
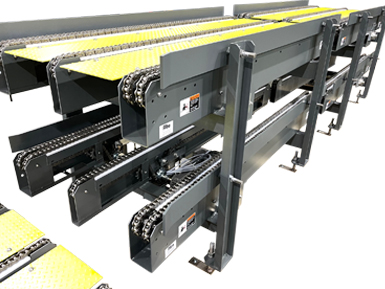
In addition to the use of stainless-steel fasteners and jack bolt feet, Alba used zinc-plated steel spacers to space out all tread plates, guide angles and support angles so these surfaces would be open for cleaning. The drag chain frame rails were designed with large drain cutouts at the bottom surface so that moisture and water could escape. Frames and legs were fabricated with full welds across all adjoining surfaces. Wear strips were machined from Nylatron GS instead of UHMW for better wear life.
The Results
Alba provided a solution for this tough application by working with the customer and supplying alternative components to stainless steel to bring about a more cost-efficient design while maintaining a very robust conveyor construction. The end user now has a solution that fits their needs.
Alba provided value by helping them develop this design for the aesthetic, functional, safety, and maintenance challenges they presented while still staying true to the Alba rock-solid conveyor!
Conveyor Specifications
- Fifteen (15) Over/Under Model DC-R80-5S x 7′-6” Long Five-Strand Drag Chain Conveyors with 2.25”-15.75”-15.75”-2.25” Chain Centers, 60 FPM, and 24”/47” Top of Chain Elevations.
- Two (2) Model DC-R80-5S x 4’-6” Long Five-Strand Drag Chain Conveyors with 2.25”-15.75”-15.75”-2.25” Chain Centers, 60 FPM, and 24” Top of Chain Elevation.
- Two (2) Model DC-R80-5S x 10’-0” Long Five-Strand Drag Chain Conveyors with 2.25”-15.75”-15.75”-2.25” Chain Centers, 60 FPM, and 24” Top of Chain Elevation.
- One (1) Model DC-R80-5S x 7’-0” Long Five-Strand Drag Chain Conveyor with 2.25”-15.75”-15.75”-2.25” Chain Centers, 60 FPM, and 24” Top of Chain Elevation.
- Two (2) Over/Under Model DC-R80-5S x 6’-10” Long Five-Strand Drag Chain Conveyors with 2.25”-15.75”-15.75”-2.25” Chain Centers, 60 FPM, and 24” Top of Chain Elevation.
- Four (4) Model DC-R80-5S x 15’-0” Long Five-Strand Drag Chain Conveyors with 2.25”-15.75”-15.75”-2.25” Chain Centers, 60 FPM, and 47” Top of Chain Elevation.
- Two (2) Model DC-R80-5S x 11’-0” Long Five-Strand Drag Chain Conveyors with 2.25”-15.75”-15.75”-2.25” Chain Centers, 60 FPM, and 47” Top of Chain Elevation.
- One (1) Model DC-R80-5S x 5’-8” Long Five-Strand Drag Chain Conveyor with 2.25”-15.75”-15.75”-2.25” Chain Centers, 60 FPM, and 47” Top of Chain Elevation.
- Fifteen (15) Model DC-R80-5S x 4’-6” Long Five-Strand Drag Chain Conveyor Top for Customer Supplied Scissor Lift Base with 2.25”-15.75”-15.75”-2.25” Chain Centers, 60 FPM, and 24”/47” Top of Chain Elevations.
- Three (3) Over/Under Model DC-R80-5S x 6’-0” Long Five-Strand Drag Chain Conveyor Tops for Customer Supplied T-Car Base with 2.25”-15.75”-15.75”-2.25” Chain Centers, 60 FPM, and 24”/47” Top of Chain Elevations.
- Three (3) Model DC-R80-5S x 5’-6” Long Five-Strand Drag Chain Conveyor Tops for Customer Supplied Transfer Conveyor Base with 2.25”-15.75”-15.75”-2.25” Chain Centers, 60 FPM, and 24” Top of Chain Elevation.
About Us
Alba Manufacturing, established in 1973, engineers and designs heavy-duty roller conveyor systems. Our systems consist of chain driven live roller (CDLR), zero pressure accumulation, drag chain, gravity, lift and rotate, pallet stackers and dispensers, turntables, chain transfers and transfer cars. Our corporate office and manufacturing facility is located in Fairfield, Ohio, approximately 30 minutes north of Cincinnati, Ohio.
For more information regarding this application/solution, please contact us via phone at 866.252.2634; via web at www.albamfg.com or via email at RockSolidConveyor@albamfg.com.