Background
Our partner’s client is a private contractor for a machine tending project. “What’s machine tending?” you ask. “Machine tending” is a process which utilizes robotics to introduce raw parts to a pre-programmed machine, removes the part once the process is complete and then introduces the next part to continue the cycle.
In the marketplace, machine tending constitutes the largest use of collaborative robots, also known as cobots. These are robots that can be used without machine guarding or without including other safety features. Cobots can be placed beside a machine or a person and set to perform a specific task without needing to be fenced off from the surrounding environment. Generally speaking, robots fulfill three goals: expand production, handle higher-value tasks and ensure safety.
Product: 32″ x 48″ steel containers, each weighing 6,300 lbs. The steel pallets, utilized in a captive system, have a “picture frame” bottom runner configuration.
Problem
The replacement cost can range anywhere from hundreds to thousands of dollars for custom-engineered pallets. Many operations require multiple pallets to be on hand and used in the process in a 24/7 manufacturing environment. If these custom-engineered pallets become lost, damaged or “taken,” the cost can become exorbitant for the end-user as production comes to a halt.
Alba and our partner needed to provide a solution to help reduce double handling of pallets; which ultimately, resulted in overuse and abuse. The end-user, caught in a vicious cycle, had to regularly purchase new and expensive tubular steel pallets since the heavy loads were taking their toll.
Solution
Alba and our partner provided a solution consisting of a robotic system to empty the containers and two (2) frame-to-frame transfers. This solution allowed the end-user to keep rotating and to utilize their tubular steel pallets more efficiently and effectively.
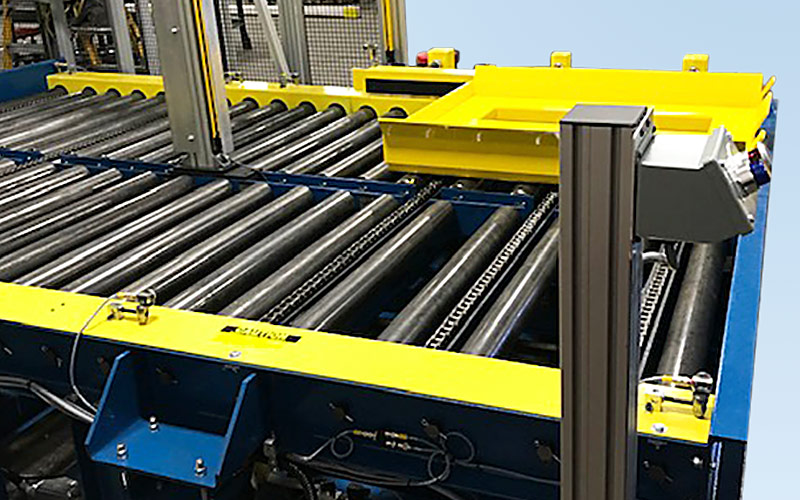
Results
By rotating the pallets and keeping them within the system, we helped the end-user save valuable “cost of doing business” dollars and reallocate those dollars to other areas of concern within their plant. With the new system, tens of thousands of dollars could potentially be saved and reallocated.
About Us
Alba Manufacturing, established in 1973, engineers and designs heavy-duty roller conveyor systems. Our systems consist of chain driven live roller (CDLR), zero pressure accumulation, drag chain, gravity, lift and rotate, pallet stackers and dispensers, turntables, chain transfers and transfer cars. Our corporate office and manufacturing facility is located in Fairfield, Ohio, approximately 30 minutes north of Cincinnati, Ohio.
For more information regarding this application/solution, please contact us via phone at 866.252.2634; via web at www.albamfg.com or via email at RockSolidConveyor@albamfg.com.