Problem
A key challenge in any production process is maintaining a perfect balance between efficiency, speed, and safety. Our integration partner, Sun Volt Systems, was tasked with fully automating a quality control, deburring, and loading process for steel tubes used in the production of washing machines by a leading appliance manufacturer.
Sequence and Solution
Metal totes, weighing 200 pounds each, are transported and filled with sticks of raw, half-inch square tubes. Once loaded, these totes weigh up to 2,500 pounds each.
The raw steel tubes enter the system at a rapid rate approaching one per second. After going through an automated quality control process rejecting “out of spec” tubes, the “in spec” tubes are automatically deburred, picked by a robot, and placed in steel totes, 40 tubes at a time.
Empty steel totes enter the system stacked three high on Alba’s standard Chain Driven Live Roller (CDLR) conveyor. Once inducted, these totes convey to an Alba provided pneumatic blade stop, locating the totes in the destacking position.
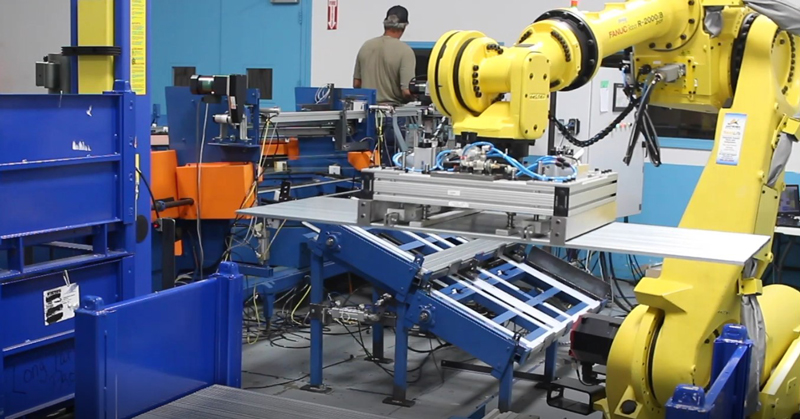
Sun Volt Systems’ unique destacking unit engages and lifts the stacked totes, allowing the single bottom tote to convey onto the tube loading position on Alba’s pneumatic turntable for the start of the robotic tube loading process.
Once each tote is filled with tubes, the turntable rotates 90-degrees and discharges totes to the stacking zone. Once again, the full totes are positioned by a pop-up blade stop and stacked three high. Finally, the stack of three full totes conveys to the pickup zone to be removed out of the system by fork truck.
Alba and Sun Volt Systems Application – Demo Video #1
The integrator required precise control of the tote’s location during tote destacking and stacking as well as the robotic tube loading process. In the tote destack/stack zones, the leading edge is aligned with a pop-up blade stop allowing consistent location for the stacking units to engage the tote’s fork pockets.
In the robotic/tube loading zone, the tote’s position on the conveyor as well as the turntable’s rotational location needed to be exact for the robot to properly load the totes. The tote’s leading edge is controlled by a fixed end stop and is side justified by a pneumatic side pusher mounted to the turntable’s top plate. The rotational position of the turntable is controlled with an adjustable rubber hard stop.
End Result
Sun Volt’s end-client, the appliance manufacturer, fully automates the previously labor intensive and tedious tube prepping process, allowing valuable production team members to be redeployed to other areas while increasing overall production and safety.
Alba and Sun Volt Systems Application – Demo Video #2
About Us
Alba Manufacturing, established in 1973, engineers and designs heavy-duty roller conveyor systems. Our systems consist of chain driven live roller (CDLR), zero pressure accumulation, drag chain, gravity, lift and rotate, pallet stackers and dispensers, turntables, chain transfers and transfer cars. Our corporate office and manufacturing facility is located in Fairfield, Ohio, approximately 30 minutes north of Cincinnati, Ohio.
For more information regarding this application/solution, please contact us via phone at 866.252.2634; via web at www.albamfg.com or via email at RockSolidConveyor@albamfg.com.