A mainstay of manufacturing is the CNC machine. The type of cutting can vary from plasma cutting to laser cutting, milling, routing, and lathes. They provide zero defects and greater accuracy, enhanced personnel safety, and eliminate unnecessary waste. CNC machines easily cut materials such as wood, metal, cardboard, stone, plastic, and even fabric.
Our case study application involves clothing material – specifically, using CNC technology to pre-cut fabric before it’s shipped to a T-shirt manufacturer. The product being handled – a 45″ x 45″ x 12″ corrugated tray, weighing a maximum 500 pounds.
Working jointly with our system integrator, Alba streamlined the end user’s manufacturing process. Rooted in the clothing apparel industry, the end user has fifty (50) cutting tables that are 4′ wide and 130′ long.
An overhead machine moves back and forth and layers fabric on the table up to 40” high. The fabric then goes into an automated CNC cutting machine which cuts out T-shirt patterns. After cutting, the material is bundled and placed into corrugated trays.
The trays of fabric are placed on an Alba manufactured cart with gravity roller conveyor mounted on top. The operator then pushes the cart to the main conveying line where it’s conveyed onto a Through-Drive Side Transfer (TDST). The tray is conveyed on the main trunk line to an automatic stretch wrapper. The stretch wrapped trays are then moved to the warehouse for shipment to a T-shirt manufacturer.
Primary Challenges
- Moving the 500-pound trays: getting the product from 50 cutting tables to the conveyor line quickly and safely. With our system integrator, Alba manufactured a cart with gravity roller to move the totes to the conveyor line.
- Loading the trays given the number of tables, the system required multiple entry points to get the totes onto the main trunk line. Alba supplied several TDSTs to allow the operators to load in multiple areas located close to their fabric tables.
Working in tandem with our system integrator, Alba’s conveying system created excellent product flow from the cutting tables to the stretch wrapper. The use of Through-Drive Side Transfers (TDSTs), Motorized Zero Pressure Accumulation (MZPA) conveyors, Turntables, and Chain Driven Live Roller (CDLR) conveyor delivered product to the stretch wrapper easily and efficiently. As a result, the customer now has a conveying system that streamlines their manufacturing process, increasing safety, efficiency, and throughput.
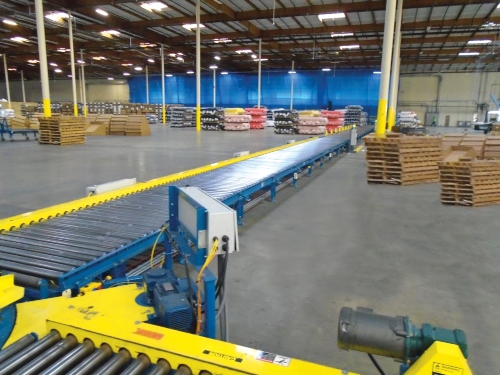
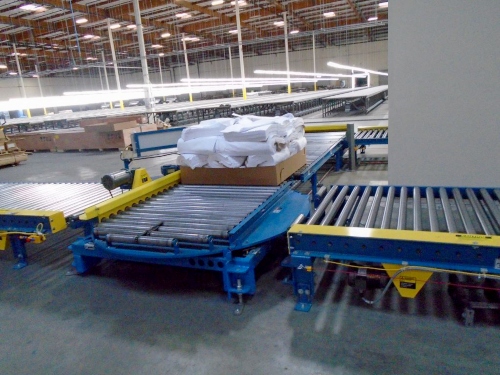
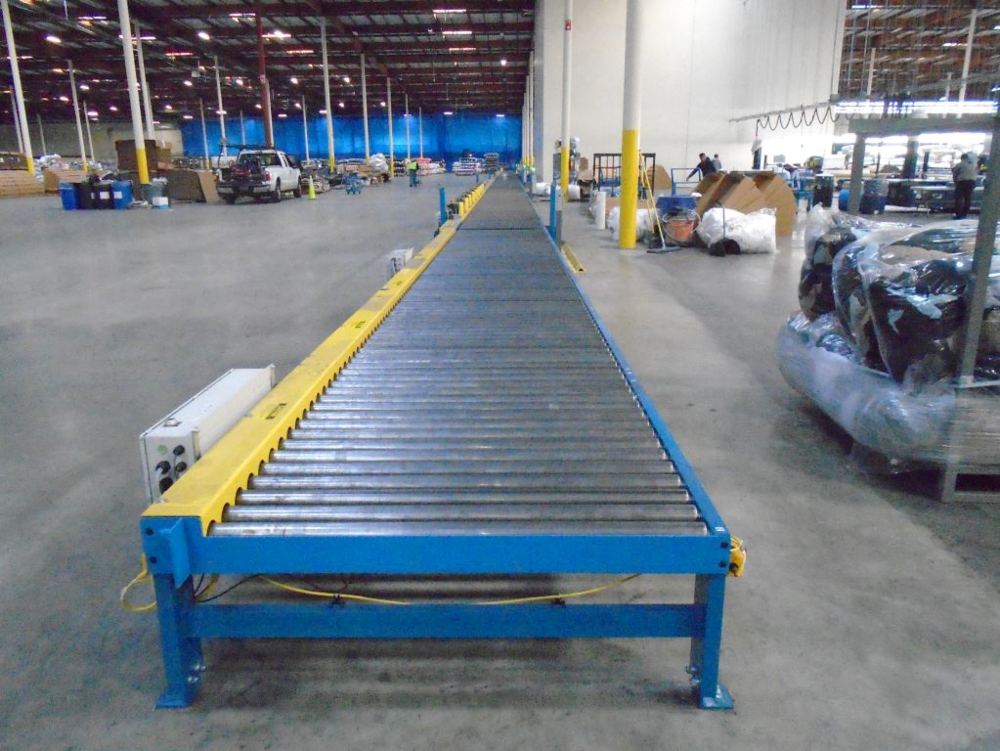
Conveyor/Product Specifications
Alba supplied Motorized Zero Pressure Accumulation (MZPA) conveyor, Low profile CDLR conveyor mounted to a motorized base, CDLR conveyor with Through-Drive Side Transfer (TDST), CDLR conveyor with Through-Frame Transfer (TFT), CDLR conveyor mounted to a lift table, Gravity conveyor, and push carts with Gravity conveyor mounted on top.
- Model MZPA251140-4 CDLR Conveyor Specifications: 35′ long with (7) 5′ zones, 49″ effective width, 4″ roller centers, 1/2 HP Baldor Motor with Dodge Tigear II Reducer, 30 fpm, 20 5/8″ top of roller sloping down to 18″ top of roller.
- Model MZPA251140-4 CDLR Conveyor Specifications: 52′ long with (9) 5′ zones, and (1) 7’0″ zone, 49″ effective width, 4″ roller centers, 1/2 HP Baldor motor with Dodge Tigear II Reducer, 30 fpm, 18″ top of roller.
- Model TDST251140-4-3S Through-Drive Side Transfer Specifications: 5′ 1-1/2″ long CDLR conveyor, 52″ effective width, 24VDC Itoh Denki powered roller with CB-0167 drive card, 30 fpm, 18” top of roller, 3-strand transfer with chains on 17″ centers, 6″ beyond inside frame on drive and non-driven side of conveyor, 2-5/8″ above the rollers when raised, 3/4 HP Baldor motor with Dodge Tigear II Reducer, 30 fpm, 20 5/8″ top of chain in raised position.
- Model TFT251140-4-3S Through-Frame Transfer Specifications: 5’2″ long CDLR conveyor, 49″ effective width, 4″ roller centers, 1/2 HP Baldor motor with Dodge Tigear II reducer, 30 fpm, 12″ top of roller, 3-strand transfer with chains on 18″ centers, 6″ beyond inside frame on non-driven side, 3/4 HP Baldor Motor and Dodge Tigear II Reducer, 12-3/4″ top of chain in the raised position.
- Model 251140-4 CDLR Conveyor Mounted to an LS4-36WHC Southworth Lift Table Specifications: 5′ long CDLR conveyor, 49″ effective width, 4″ roller centers, 1/2 HP Baldor Motor with Dodge Tigear II Reducer with high side mount motor, 30 fpm, 12-3/4″ top of roller mounted to lift table in lowered position. High Cycle Southworth Lift Table, 4,000 lb capacity, 36″ of vertical travel.
- Model TT251140-4 CDLR Conveyor Mounted to Low Profile Turntable Base Specifications: 78″ diameter, 49″ effective width, 4″ roller centers, 1/2 HP Baldor Motor with Dodge Tigear II Reducer, 30 fpm, 12-3/4″ top of roller, with 3 sets of floor mounted transition rollers, turntable base chain driven via 1 HP outboard mounted Baldor Super “E” Motor with Winsmith Gear Reducer.
- Model 251SS-3-49 Gravity Conveyor: 30′ long, 49″ between frame, 3″ roller centers, rollers set 3/4″ low in the frame, 36″ top of roller.
Value Added Features
- Pin Stops on Through Drive Side Transfer
- Photo Eyes and Proximity Switches mounted to the conveyor and wired to a junction box
- Wheel Stops
- Full controls on MZPA conveyors with plug and play technology for easy installation in the field
About Us
Alba Manufacturing, established in 1973, engineers and designs heavy-duty roller conveyor systems. Our systems consist of chain driven live roller (CDLR), zero pressure accumulation, drag chain, gravity, lift and rotate, pallet stackers and dispensers, turntables, chain transfers and transfer cars. Our corporate office and manufacturing facility is located in Fairfield, Ohio, approximately 30 minutes north of Cincinnati, Ohio.
For more information regarding this application/solution, please contact us via phone at 866.252.2634; via web at www.albamfg.com or via email at RockSolidConveyor@albamfg.com.