Vending Machines Mean Big Business |
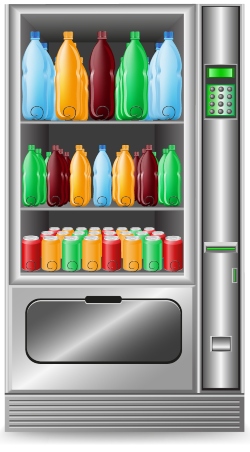 |
|
Vending machines have been a part of the American scene since 1888, when the first stick of tutti-frutti gum was dispensed and sold in a New York City subway. Established as early as 1926, the most popular, fully automated commercial dispenser was the soda vending machine. By the 1950s, legendary brand name soda producers dominated the market selling their bottled, sugary elixirs1. Now with an estimated 4.6 million vending machines in the U.S. (2017), the annual spend tops $7 billion annually, with 56% of sales consisting of cold drinks.2
Application and Challenges |
April’s application involves refurbishing and cleaning 600 lb. soda vending machines on 40" x 96" or 40" x 60" carrier boards. Dealing with any bulky, heavy objects safely and ergonomically is always a challenge. Other requirements included: |
• |
Operator processing required vending machines to remain at a low elevation. |
• |
Due to an upstream washing process, conveyor needed to be corrosion resistant. |
• |
Vending machines needed to be easily transferred 90-degrees from a trunk line onto operator workstation spurs. |
• |
Once located in a workstation spur, the vending machine needed to remain stationery and stable during the work process. |
|
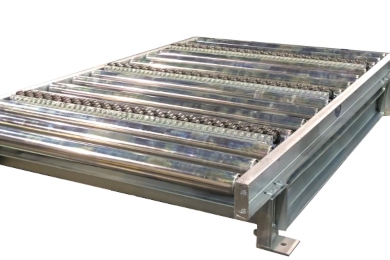 |
|
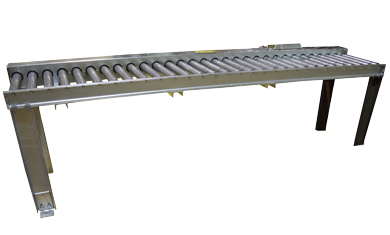 |
To keep the lowest elevation possible and provide maximum control, Alba used standard gravity conveyor equipped with pneumatically actuated Superail transfers. These transfers allowed the product to be moved safely to the operator work stations. Pneumatic actuated roller brakes in the work zones ensured product stability during the operator work process. Lastly, to affordably address the moisture issue, Alba’s hot dipped, galvanized frame and supports zinc plated rollers and sealed bearings, allowed the conveyor to handle residual moisture from the recently washed vending machines; thereby resisting corrosion.
Alba’s integrated, full-length gravity conveyor line allows for a stable and ergonomic method of transporting and queuing vending machines during the cleaning and refurbishment process, ensuring product and operator safety.
Conveyor/Product Specifications |
• |
Length: 100’ Systems Overall Length |
• |
Rollers: 2-1/2" diameter x 11-gauge zinc plated tubing, with 11/16" zinc plated hex axles, spring retained, and ABEC-1 sealed bearings |
• |
Effective width: 44" |
• |
Elevation: 11" Top of Roller |
• |
Paint: Hot dipped galvanized frames and zinc plated rollers |
Value Added Features |
• |
Pneumatic Transfer: Three (3) 43-1/4" long Superails (by Darnell-Rose) on 24" centers, pneumatically raised 3/4" above the rollers. |
• |
Between Roller Tread Plates: Zinc plated diamond tread plate installed between rollers creating cross over zones. |
• |
Roller Brake: Includes one (1) 40" long friction brake pad assembly with pneumatic actuation. |
If you need creative and rock-solid solutions, call Alba Manufacturing at 866.252.2634 or visit our website at www.albamfg.com. We will collaborate with you to supply the maximum, most efficient, and cost-effective system(s) available.
1 https://vendingone.com/what-did-the-first-vending-machines-in-the-us-dispense
2 https://brandongaille.com/23-intriguing-vending-machine-sales-statistics
If you missed us at MODEX 2020, Alba’s very own, Brad Bell gives an overview of what Alba is all about. It takes about a minute. Take a look!
Click to View the Video |
|
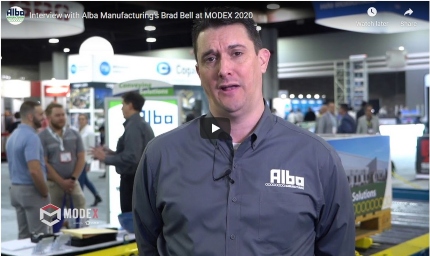 |
Follow Us on Social Media! |
 |
|