Nerves SHOT Over Challenging Projects? Let Alba BLAST Away Your Worries in 2022. |
As communities continue to fight the pandemic, US hot-rolled steel prices are up 225% as compared to pre-pandemic levels1. In March 2020, steel was trading between $500 and $800. As of July 2021, the price of steel was trading at $1,8252. Why? One reason is due to cutbacks in steel production by steel manufacturers for fear of a recession. Another reason is increased demand. Since consumers couldn’t spend money on vacations, they wanted steel-intensive goods such as new cars, appliances, and mowers.
To compete, both steel suppliers and distributors were forced to look for alternative sources to fulfill demand. One supplier, a customer of Pangborn Corporation in Fairborn, Georgia, decided to offer shot blasting services for large steel products purchased by their customer base.
|
|
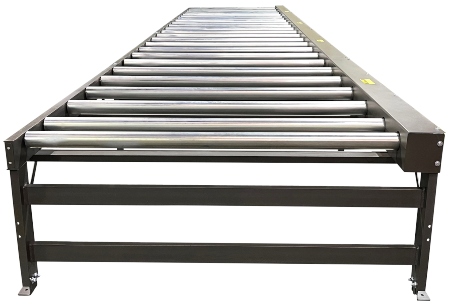 |
|
|
Pangborn, an Alba integrator/OEM partner, and manufacturer of automatic shot blasting machinery, asked Alba for help. The challenge? What was the best way to move steel through the blasting process automatically?
Pangborn’s customer, a full-service carbon steel pipe and tube distributor, needed a new Pangborn blasting machine. The automatic blasting machine fed large round, square, and plate steel products through the machine via the machine’s internal conveyor rollers. However, Pangborn needed an infeed and discharge conveyor to facilitate conveyance to and from their blasting machine.

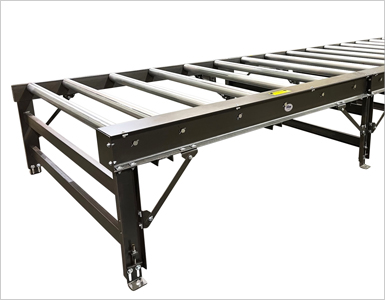 |
|
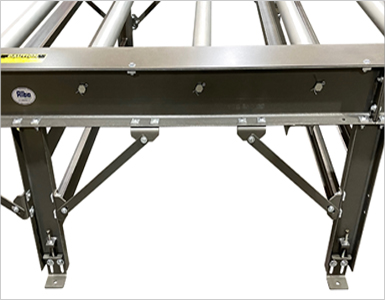 |
 Knee Braced Leg Supports with Jack Bolt Adjustable Feet |
|
Knee Bracing and Jack Bolt Adjustable Feet on Supports (Close-Up View) |
Individual parts weighed a maximum of 550 pounds per foot with a not-to-exceed conveyor load of 25,000 pounds. Alba faced two primary challenges. One, to convey large and heavy steel parts successfully, and safely. Two, since the facility is located outdoors in the Midwest, without a building or roof system, the conveyor application required extra safeguard against the elements.
Alba determined the best solution to protect the conveyor by adding zinc plated rollers, axles, sealed precision bearings, gearmotors with IP-66 rating, and low temperature oil rated for -4° to 140°F. All chains provided were Aqua Series® coated roller chain. All frames and leg supports were painted with a Steel-It® brand epoxy paint. These add-ons provided an upgrade to the protection and finish of the conveyor to withstand the harshest of outdoor environments.
 |
|
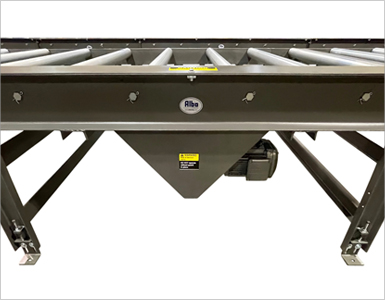 |

1.9” Diameter Sensor Roller (Spring Loaded) Shown Next to 3-1/2" Diameter Heavy-Duty Rollers |
|
Under Slung Drive, Pinned Axle Style Rollers, and Jack Bolt Adjustable Feet |
Alba Infeed Section (outside): a 35-foot conveyor section fed by another conveyor where steel product was loaded by crane. To control the production flow, Alba provided an old-style sensor roller that was spring-loaded and depressed when the steel parts conveyed over it. Once this sensor depressed, a connected proximity sensor would provide a signal to the blasting machine indicating that the part was close to the blast cabinet. The wheels would start throwing shot material so the parts could be blasted upon entering the cabinet. After the sensor roller returned to its original "up" position because the steel part had conveyed to a point beyond the roller, it would allow Pangborn to start their control timer. This timer, once expired, would stop the flow of the blasting material inside the cabinet.

Alba Discharge Section (outside): another 35-foot conveyor section that received finished steel parts from the blast machine. Steel parts were delivered to a downstream conveyor and off-loaded by crane. On the discharge conveyor section, Alba provided a solid roller at the infeed end. It extended beyond the frame at one side as a round, keyed auxiliary shaft. Pangborn used the conveyor-driven shaft to drive their internal cabinet rollers.
On the infeed of the takeaway and discharge end of the feed conveyors, near the cabinet, Pangborn had a spill hopper underneath our conveyor where excess shot medium was reclaimed and recirculated back to the throwing wheels by use of a screw conveyor (by Pangborn). Alba provided all chain guards with slots machined in the bottom halves to relieve any buildup of blasting grit.
Alba and Pangborn collaborated to create a solid automated solution. The end user, Pangborn’s customer, continues to successfully compete within the ever-changing steel landscape while providing additional products, value, and services to the marketplace. |
|
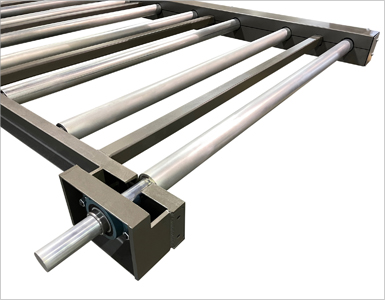 |
Solid Roller with Outboard Bearings and Shaft Extension Used to Drive Customer’s Internal Cabinet Rollers
|
|
Conveyor/Product Specifications |
• |
(2) Model 353080-18 Chain Driven Live Roller (CDLR) Conveyors x 35'-0" Long |
• |
76" Effective Conveying Width |
• |
3-1/2" Diameter x 0.300" Wall Rollers with 1-1/16" Pin-Retained Hex Axles (Zinc-Plated) |
• |
18" Roller Centers |
• |
RC80 Aqua Series Roller Chains |
• |
ABEC-1 Precision Bearings, Grease Packed |
• |
Rollers Set 1-3/4" Low (Drive Side) & 3/8" High (Non-Driven Side) |
• |
2HP SEW Gearmotor with Severe Duty Rating, IP-66, Low Temperature Oil |
• |
Under Slung Drive with Double Single Driver Sprocket |
• |
UHMW Wear Strips Added to Bottom of Scallop Guards (Due to Long Roller Centers) |
• |
One (1) Sensor Roller on Infeed Conveyor with 24VDC Proximity Sensor, Bracket and Cable |
• |
One (1) Solid Roller with Flange Bearings and Extended Keyed Shaft |
• |
Speed: 20 FPM @ 60 Hz. |
• |
Elevation: 59" Top of Roller |
• |
Eight (8) Supports per 35' Section with Knee Bracing and Jack Bolt Adjustment |
• |
Paint: Steel-It® Epoxy |
For rock-solid solutions and conveyor systems, contact Alba Manufacturing today at 866.252.2634 or visit our website at www.albamfg.com.
1Article from Source Link.
2Article from Source Link.
Follow Us on Social Media! |
 |
|