TAB Industries, a manufacturer of quality stretch wrapping machines and home of the TAB Wrapper Tornado orbital stretch wrapper, reached out to Alba for a unique solution on a project that involved entrance and exit conveyors for one of their wrapper systems. TAB is a long-time, valued partner of Alba Manufacturing. This project was designed to convey palletized loads of custom toolboxes and tool drawers from a manufacturer that serves many industries including work van customization, public service vehicles and even the car racing industry.


This application posed a certain challenge of not only conveying 3,000-lb. full pallets through a TAB orbital wrapper from their "Perfect Storm" line of wrappers, but also required cross wrapping the pallets before exiting and finally capturing the net weight of the load before the pallets were unloaded from the conveyor. Alba utilized a couple of different designs in this application to solve these challenges. First, the Alba Lift and Rotate Conveyor was utilized on the front end of the system to allow conveyance into the wrapper in one direction. Then the load was reversed back onto the lift and rotate to turn the pallet 90° and then be conveyed back through the wrapper to be cross-wrapped with a second layer of film.
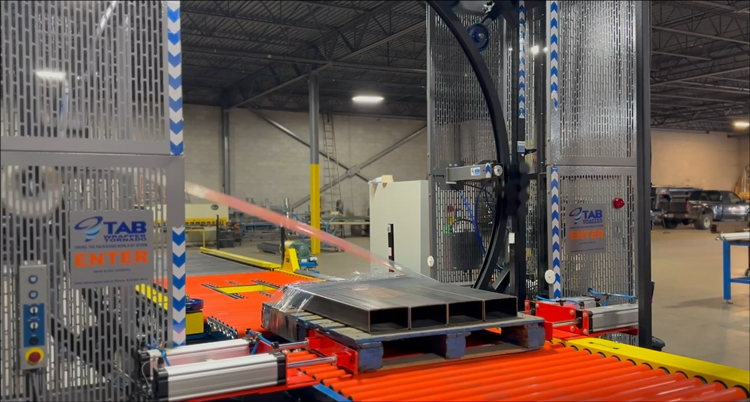 |

Alba’s rollers were coated with orange urethane sleeves to ensure good contact and a non-slip surface and to minimize movement of the pallet while the stretch wrapper was applying the film. TAB Industries added an anti-fishtail device to also control movement of the pallet each time the pallet was being wrapped. This device used a series of cylinders to apply a light force at the rear of each pallet as it was conveyed through the wrapping machine. This allowed the pallet to remain square to the conveying surface as the film was applied and eliminated any side skewing of the pallet caused by the force of the film itself.
Once the pallets were fully wrapped in each direction, they were conveyed to the exit conveyor. This end user had a requirement that each pallet needed to be weighed and the weight recorded prior to being unloaded from the wrapping line. To achieve this, Alba added a series of load cells to each leg on the exit conveyor which were wired back to a summing junction box and then onto a digital indicator allowing an operator to record the weight of each pallet prior to the end user’s robot side unloading the unitized product from the conveyor line.
Integrating the load cells and digital indicator directly on the conveyor itself, made it easier and faster for the operator to complete the wrapping process and avoided handling the pallet in a secondary weighing operation on an external scale thus saving time.

Ultimately the customer’s requirements were satisfied by this design, with the added benefit of not having to handle the loads multiple times to achieve their goal. To see how you could utilize this on your future projects, please contact Alba or TAB Industries or visit either www.Albamfg.com or www.TabWrapper.com today!

|