Automation – A Solution to Increased Demand, Labor Shortages & Safety Concerns |
|
A leading manufacturer of chemicals was seeking a way to automate their drum and intermediate bulk container tote filling operations. Their current method involved fork trucks, pallet jacks and a tremendous amount of labor to transport empty and full containers of product throughout their production and warehouse areas. This process was time consuming and a safety hazard to their employees due to the amount of traffic in their plant.
As production and demand for their product increased, so did the opportunity for accidents while transporting their product from the production side to the warehouse side for shipment. |
|

|
In addition to production increases, they had difficulties in finding and hiring new employees to fill the open positions. They sought an automated solution to receive incoming pallets of empty drums and IBC containers to feed the filling process and a way to deliver the filled containers to the warehouse for shipping.
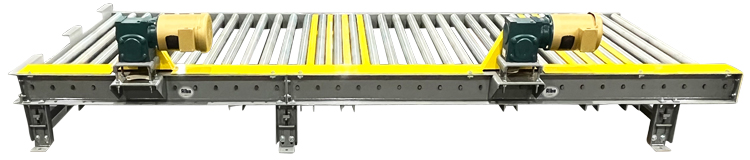 |
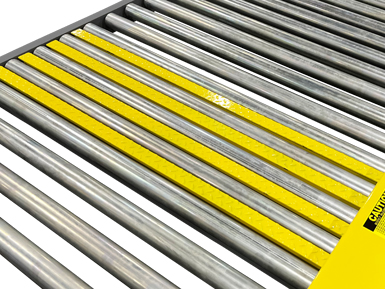 |
|
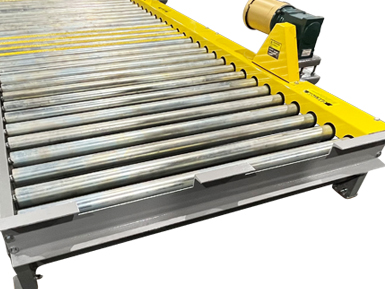 |
One of Alba’s partner OEM equipment integrators, an automated filling machine manufacturer, was selected for the project. The concept was to have a single fork truck driver deliver empty IBC containers or pallets of 55-gallon empty barrels to an infeed drop-off zone. Once the pallet/IBC container is dropped-off, the conveyor/filling controls would take over and accumulate empty containers down to the fill zone.
At the fill zone, the conveyor is mounted on a floor scale for measuring the weight before and after the filling of the containers. The conveyors adjacent to the fill zone are affixed with tread plates mounted between the rollers allowing the operator to walk between their operator platform and the conveyor surface making it easier for the operator to affix labels and drum caps. The operator is present at the fill/scale zone to properly locate the fill spout into the container or drum and fill the container/drums with desired amount of material.
The scale is integrated into the controls and a label printing machine is provided for printing product identification and weight labels for placement onto the tote/drums. Once the containers are full, the operator caps the containers and hits a release button allowing the filled containers to exit the fill/scale zone. The filled containers are then conveyed and accumulated down the line of conveyors and then unloaded via fork truck and transported to the warehouse for storage and shipment. |
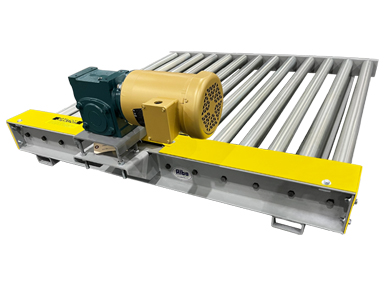 |
|
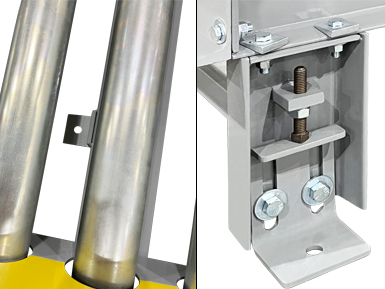 |
Alba provided CDLR conveyor with cross over treads and supports to an elevation of 13-1/2" and a CDLR with mounting tabs to allow the customer to mount the conveyor to their scale with a finished elevation of 13-1/2". The equipment was manufactured in Alba’s plant in Fairfield, OH. The equipment was then checked for quality and shipped out to the integrator for complete integration into the system. The integrator provided the filling equipment as well as the controls for product accumulation, filling, and weighing the loads. Once the Alba equipment was received, it was married to the integrators controls in preparation for a complete system run-off.

Alba worked with the integrator to design and build a system that was flexible, robust, and efficient to satisfy the customer’s needs.
Conveyor/Product Specifications |
• |
251160-4.5-52 CDLR Conveyors 2-1/2" x 11 Gauge, 52" EW |
• |
Zinc Plated Rollers and Sprockets |
• |
Color Match Paint to the Integrator’s RAL Number |
• |
Jack Bolt Adjustable Feet |
• |
Two (2) Bolt on Structural Steel End-Stop with Fork Cutouts |

Alba Manufacturing is your full-service, conveyor manufacturer for all your pallet handling applications. Call us to locate your nearest Alba Partner Network Member to assist with your next project at 866.252.2634 or visit our website at www.albamfg.com to discuss.
|