Scrubbing the Inefficiencies Out of Appliance Manufacturing |
Our integration partner, Sun Volt Systems, was tasked with fully automating a quality control, deburring, and loading process for steel tubes used in the production of washing machines by a leading appliance manufacturer.
Metal totes, weighing 200 lb. each, are transported and filled with sticks of raw, half-inch square tubes. Once loaded, these totes weigh up to 2,500 lb. each.
The raw steel tubes enter the system at a rapid rate approaching 1 per second. After going through an automated quality control process rejecting "out of spec" tubes, the "in spec" tubes are automatically deburred, picked by a robot and placed in steel totes, 40 tubes at a time.
Empty steel totes enter the system stacked three high on Alba’s standard CDLR conveyor. Once inducted, these totes convey to an Alba provided pneumatic blade stop, locating the totes in the destacking position. |
|
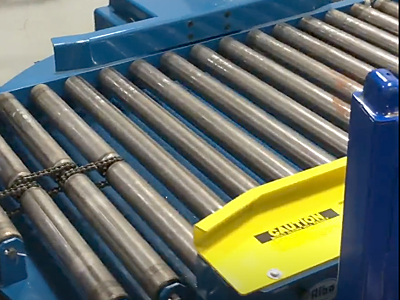 |
Sun Volt Systems' unique destacking unit engages and lifts the stacked totes, allowing the single bottom tote to convey onto the tube loading position on Alba’s pneumatic turntable for the start of the robotic tube loading process.
Once each tote is filled with tubes, the turntable rotates 90-degrees and discharges totes to the stacking zone. Once again, the full totes are positioned by a pop-up blade stop and stacked three high. Finally, the stack of three full totes is conveyed to the pickup zone to be removed out of the system by fork truck.
The integrator required precise control of the tote’s location during tote destacking and stacking as well as the robotic tube loading process. In the tote destack/stack zones, the leading edge is aligned with a pop-up blade stop allowing consistent location for the stacking units to engage the totes' fork pockets.
In the robotic, tube loading zone, the tote’s position on the conveyor as well as the turntable’s rotational location needed to be exact for the robot to properly load the totes. The tote’s leading edge is controlled by a fixed end stop and is side justified by a pneumatic side pusher mounted to the turntable’s top plate. The rotational position of the turntable is controlled with an adjustable rubber hard stop.
In the end, the appliance manufacturer fully automates their previously labor intensive and tedious tube prepping process, allowing valuable production team members to be redeployed to other areas.
 |
|
 |
Conveyor/Product Specifications |
• |
Length: 5'4" Overall Length of Straight Conveyor Sections |
• |
Rollers: 2-1/2" Diameter x 11-Gauge Wall, 11/16" Hex Axles, Spring Retained, Two (2) #40A21 Sprockets, "FR" Series Grease Packed Ball Bearings |
• |
Effective Width: 36" Effective Conveying Surface |
• |
Motor: 1/2 HP, Baldor C-frame Brake Motor (VBM3538) and Dodge Tigear II Gear Reducer, 460/3/60, RC-40 Drive Chain, Under Slung Mounted Drive |
• |
Elevation: 24" Top of Roller |
• |
Paint: Alba Blue with Safety Yellow Chain Guards |
• |
Standard items included: End Stop: Fixed Channel Type; Back Stop: Mounted to the Scalloped Chain Guard; Transition Stands: Conveyor-mounted Transition Roller Stands; and Side Guides: Cantilevered Side Guides with Beveled End (both sides)
|
|
|
Value Added Features |
• |
Empty Tote Pusher: Conveyors include a pneumatic operated, empty pallet, side pusher providing approximately 9-1/2" of stroke and backstop mounted to the top of the scalloped chain guard. Assembly includes one (1) 24 VDC IFM Efector Proximity Switch with 2-meter Quick Disconnect (QD) Cable to sense the pusher in the retracted/open position. Includes one (1) Norgren 24 VDC Double Solenoid Valve and Filter Regulator. |
• |
Blade Stop: Conveyors include a pneumatically operated support mounted pop-up blade stop actuated via an air cylinder. Each stop includes a Norgren 24VDC Double Solenoid Valve and piped back to the appropriate cylinder with poly tubing. One IFM 24VDC Proximity Sensor (#IG7101) per stop is provided with QD Cable. Proximity senses the stop in the "raised" position only. |
|
For rock-solid solutions and conveyor systems, contact Alba Manufacturing today at 866.252.2634 or visit our website at www.albamfg.com. |
Follow Us on Social Media! |
 |
|